21世纪以来,能源危机和环保问题是全社会关注的热点,对汽车工业也提出了更高的要求。如今国内外的汽车生产商都在研究如何使汽车轻量化,其中以铝代钢是轻量化技术的首选,铝合金结构件占汽车零件的比重也越来越高。压力铸造是目前铝合金成形中材料使用率高、外观质量好,效率最高的成型方法,在汽车节能减排、以铝代钢的生产中功勋卓越。
然而,汽车缸体、离合器、汽车底盘结构件、齿轮箱等零件,利用传统高压铸造生产时,型腔内的气体来不及往外排,造成的结果是模具型腔内的卷气,进而导致铸件内部产生气孔等压铸缺陷,无法满足高抗拉强度、高屈服强度、高伸长率等力学性能指标要求。
高真空压铸可以很好的解决铸件内部气孔缺陷的问题,它既具备普通压铸的外观质量好,生产效率高,材料利用率高的特点,同时又可以满足高性能铸件的要求, 因此高真空压铸在工业生产中 ,尤其是在汽车轻量化进展过程中,扮演着非常重要的角色。
国内已有不少压铸厂家进入了结构件的研发和生产,但研究成果却罕见报端; 高强韧铝合金的性能通过试验研究已获得初步认识,并进行了报道,然而行业对高强韧铝合金的结构件生产工艺及产品的热处理研究却罕有报道,本文结合公司生产的一款汽车底盘结构件,系统介绍了高真空压铸工艺以及不同热处理工艺对产品性能的影响。
1产品开发技术要点
1.1产品外形尺寸及基本要求
产品的 3D 模型如图1所示。 其空间尺寸为 677.79mm>< 115. 40m ×232.42m, 产品浇注重量为2 .6kg, 平均壁厚约为3.5mm,铸件在分型面的投影面积为 86300m㎡。 铸件有多处位置,尤其是螺纹孔位置壁厚变化较大, 判断为热节位置, 在压铸成型时容易出现缩孔或疏松。
铸件的内部品质要求为 :一般铸造位置孔洞在Ф 1㎜ 以下, 凸台位置、肉厚位置要求Ф 2㎜ 以下;之间外观要求无明显的流痕和龟裂纹,表面不能有气泡。
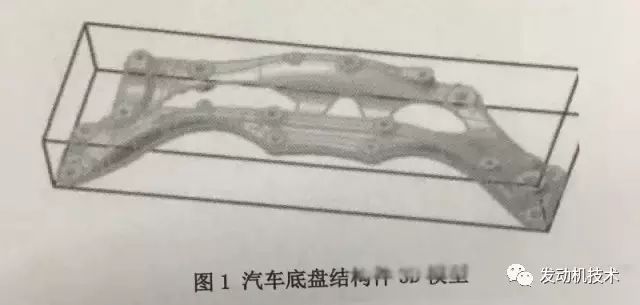
1.2压铸合金
生产所用合金为高强韧铝合金Silafont36. Silafont36合金是一种Al-Si-Mg系压铸合金,Si含量为9.5%-11. 5%,因此合金具有良好的充型性能;为获得较高的强度和韧性,严格控制Fe含量在0.15%以下,同时为解决低铁合金的粘模倾向,添加了适量的Mn; Mg含量一般控制在 0.1%、0.5%,Mg是主要的强化元素,生成Mg2Si 强化相,在时效过程中析出纳米级的Mg2Si粒子,弥散分布于基体中,显著提高铸件的强度[6]。生产中所用的Silafont36合金各成分含量如表1。
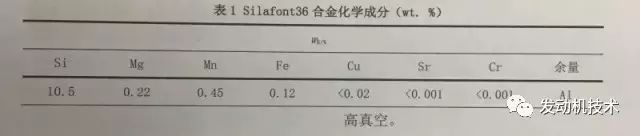
1.3压铸模具及高真空压铸工艺
模具设计压射直径为Ф130 ,充满度为22.3%。由于高真空压铸模具充满度较低,型腔 ( 含浇道)空气含量仅为料槽含量的 1 /5左右 , 因此排除料槽空气不可忽视。 压室采用整体压室 ,并在适当位置开设真空排气孔,用于排除压铸内的空气 ,压射冲头采用自密封冲头,如图2。
由于产品造型无需抽芯机构,因此对压铸模具分型面采用了耐高温胶条密封,同时模具顶针、快换型芯针以及动定模镶块均采用密封思路设计。 生产时采用双向高真空压铸 , 高真空阀为液压驱动主动开关阀 ,以冲头行程控制真空阀的开闭,实现半程抽高真空。
Silafont36具有良好的填充性能,但是该底盘结构件较为复杂,填充行程较长,填充过程中降温较大, 因此设定铝液温度为 670 ℃ , 采用模温机控制模具温度为 220 ℃ , 产品热节位置采用高压点冷控制。熔体的进给方式为定量炉自动进给,可以精确控制进给量和保证进给铝液温度的稳定。压铸机具有压铸参数的闭环控制功能,同时可实现对参数的实时监控,对于超出设定参数范围的产品,自动取件手可实现自动报废功能,严格监控产品品质。
生产时,模温到达合理温度区间后,由机边作业员监控产品外观质量,100%全检产品外观,保证产品无冷隔,无裂纹,无扣伤,无烧伤等缺陷,内部质量采用高分辨率x光检测机构进行过程监控,要求x光无任何气孔,疏松等。图5为产品切割成3部分后x光图片。
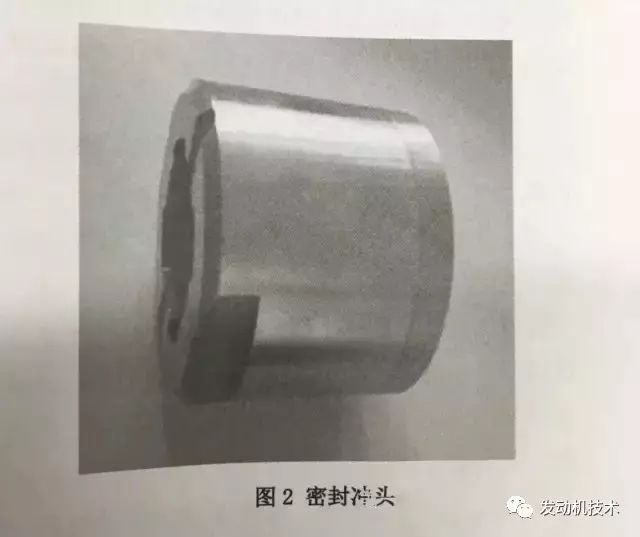
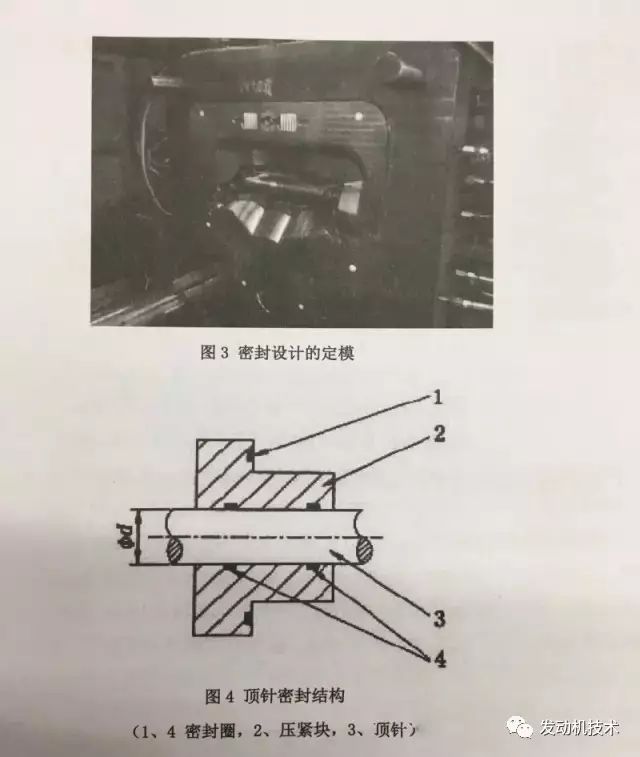
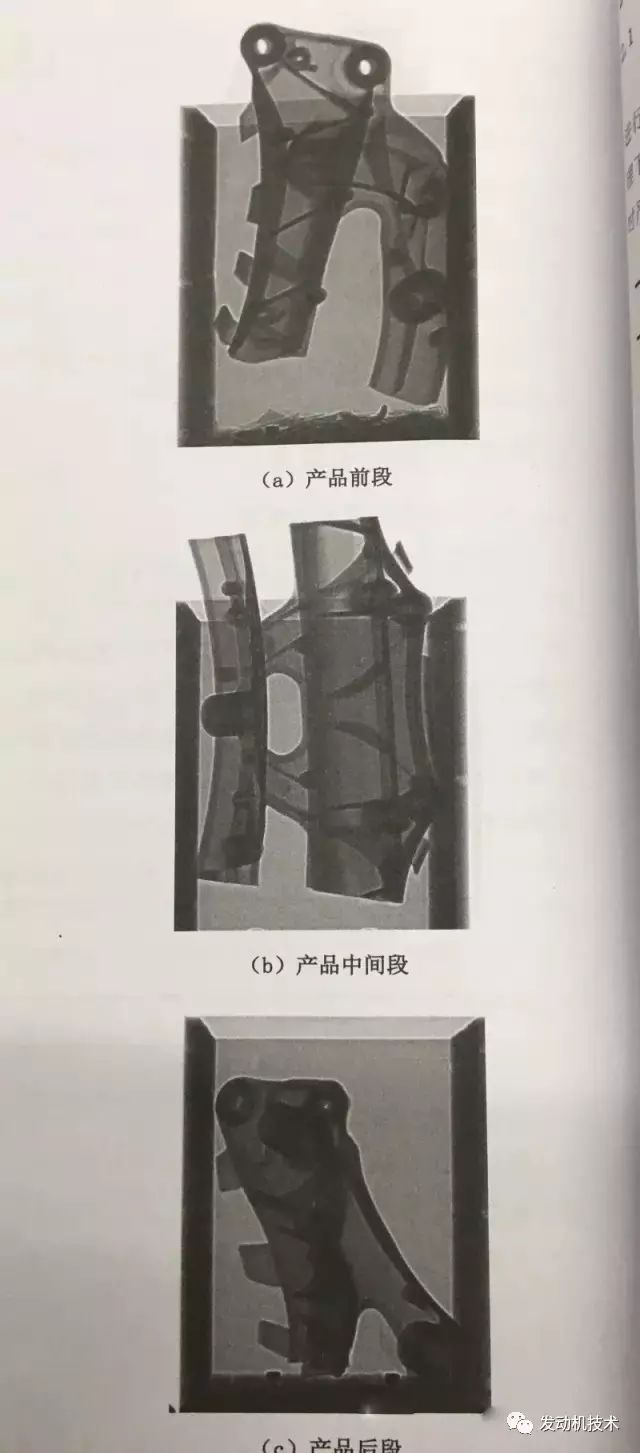
从产品的X光图片可以看出,产品内部组织致密,无疏松,无气孔缩松,这是产品可以进行T6,T7热处理的基本要求。
2 产品的热处理工艺探究
2.1热处理方案设计
一般而言,普通压铸件由于含气量高,无法进行高温处理。因为铸件中的气体在高温热处理下发生膨胀聚集,造成铸件表面亚种鼓泡,同时严重降低铸件的伸长率。采用高真空压铸时,铸件中含气量可低于15ml/100g,甚至低于10ml/100g,可以对铸件实施T6,T7热处理。
为获得Silafont36合金在不同热处理状态下的机械性能表现,在实验中,分别设计了T5、T6、T7三种热处理状态,以铸态条件下的性能表现作为参照组。T5、T6、T7热处理工艺如表2所示。
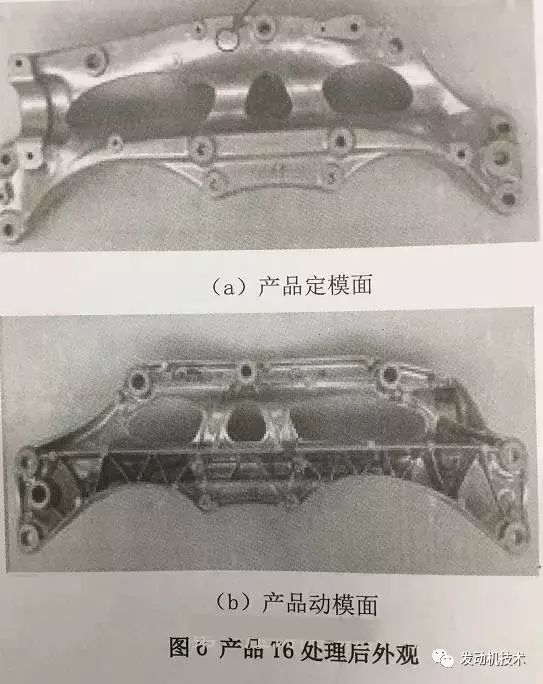
热处理在连续式热处理炉中进行。T6、T7处理时,固溶处理完毕,产品进入淬火炉,淬火完成后,产品直接被输送至时效处理炉,保证了热处理的连续性。
固溶热处理后产品的外观如图6所示,产品表面只在局部位置存在Ф0.5mm左右的鼓泡,并且数量较少,零星存在,如图7所示。
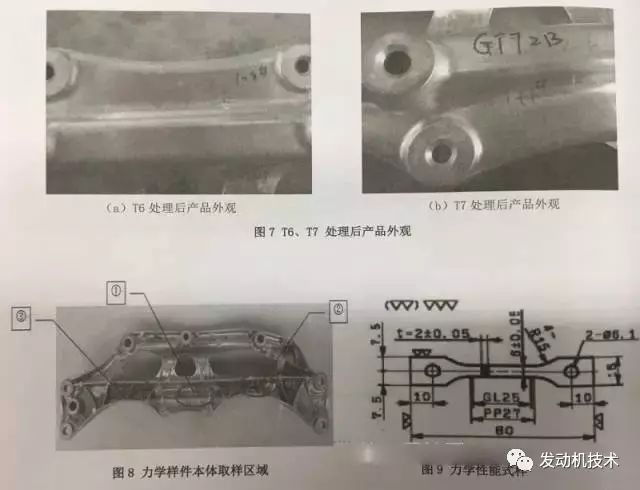
2.2高真空压铸结构件力学性能检测方案
高真空压铸结构件性能测试采取本体测试方案,取样位置产品的壁厚为3.5 ±0.5mm(,加工后试样的厚度为 2 ± 0.05mm , 从产品取样后需要将产品两侧加工去除余量。 产品本体取样位置区域标识为1.2.3然后对试样加工成测试样件,在万能拉伸试样机上进行力学性能测试。力学性能取样区域如图8所示 , 试样尺寸如图9。
2.3热处理分析结果
(1)铸态试样下的力学性能测试结果见表3。
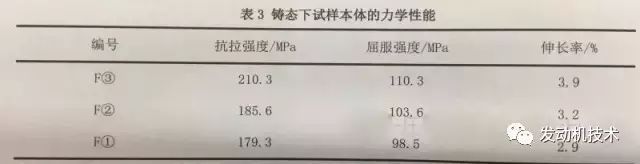
铸态下铸件随着取样位置的不同其力学性能表现不同,其中样件位置1.2.3的试样的力学性能存在差异,其中位置3抗拉强度、屈服强度和伸长率性能均优于位置1和位置2,因为位置3 处于入料口位置,增压补缩效果较好,组织较为致密,性能较好。从产品整体分析,铸态下其抗最小值为179.3MPa,屈服强度最小值为98.5MPa,而伸长率最小值为2.9%。
可见Silafont36合金铸态下力学性能较之前的研究结果[ 3]差异较大,原因为之前的研究是在试样上直接切割成力学测试试棒,铸件的致密层没有被破坏。而铸件本体取样则不然,铸件本体非规则形状,因此需要机加工去除本体试样两侧致密层后才能获得符合标准的测试样件。显然,铸件致密层对铸件性能的影响是非常显著的。
(2)T5热处理结果及分析
T5热处理试验结果如表4所示。
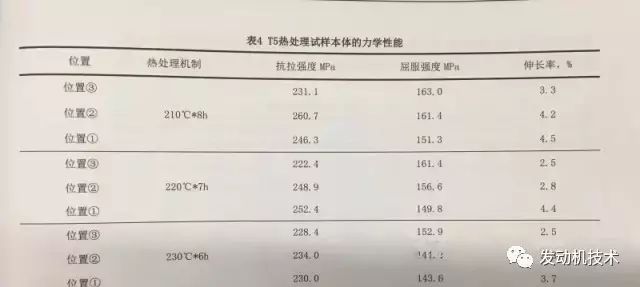
从表4可以看出,T5处理后,铸件的抗拉强度最大可达到260.7MPa,而最小值达到222.4MPa, 相比铸态下,最小值提高了43.1MPa,提高了24%,屈服强度最大值可达163MPa, 最小值可达143.6 MPa最小值比铸态下提高45.1MPa提高了45.8%,而伸长率相比,则没有明显的降低 , 最小值达到了2.5%,而最大值也达到了4.5%。在T5处理机制分析,显然,从试样力学性能分析,时效处理温度210 ℃,处理时间8小时获得力学性能较其他两组更优。
(3)T6热处理结果及分析
T6热处理试验结果如表 5 所示。
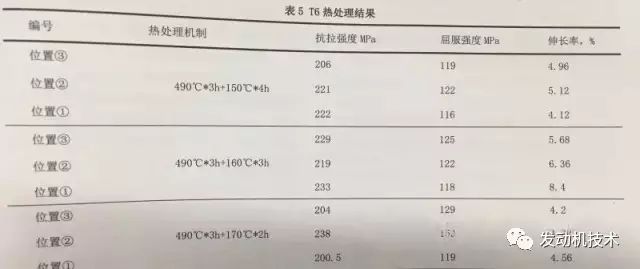
T6 处理后,铸件的抗拉强度最大值可达 238MPa,最小值为200.5MPa。与铸态相比,T6处理后,铸件抗拉强度的最小值有了较大降低,减少了21. 9MPa,降低12.2%,即使最大值也比铸态下减少了22.7MPa'降低了10.8% ,T6 处理铸件的屈服强度最小值 116MPa。比铸态最小值增加17.5MPa,提高了17.8%,然而伸长率显然比铸态下有了显著提高,T6处理后,铸件的伸长率有了较高提高,从表5中可以看出,铸件伸长率最小值达到了4.2%,最大值达到了8.4%。从T6处理工艺分析,显然固溶温度490 ℃,固溶时间3小时,时效温度160 ℃,时效时间3小时综合比较相对其他两组T6工艺较好,T6处理后铸件的抗拉强度较铸态有了降低,屈服强度略有提高,伸长率提高较为明显。
(4)T7热处理结果及分析
(5)T7处理试验结果如表6所示
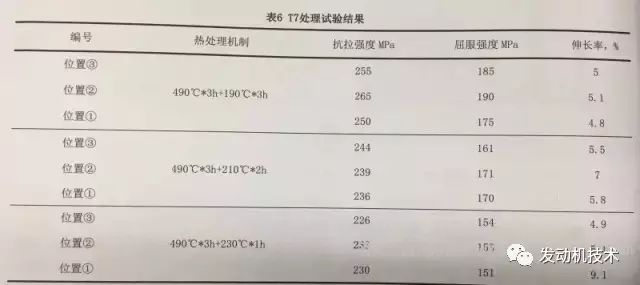
从表6可以看出,T7处理后铸件的抗拉强度和屈服强度较铸态有了明显提高,铸件的抗拉强度最大值达到了265MPa,最小值为226MPa,比铸态下铸件的最小值提高了46.7MPa,屈服强度最大值达到了190MPa,最小值也达到了151MPa,比铸态下屈服强度的最小值提高了52.5MPa,提高了53%,伸长率最小值达到了4.8%,最大值也达到了9.1%。
在工艺设计的范围内 ,不同的热处理状态下铸件的屈服强度和伸长率的变化关系如图 10所示。
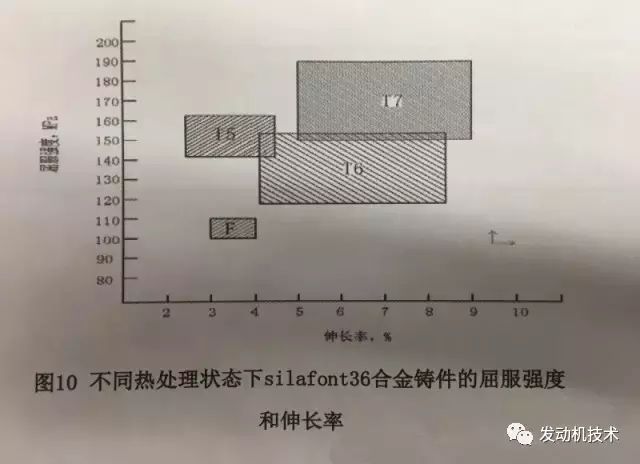
从图 11 可以看出,T5处理、 T6 、 T7 处理均可提高铸件的屈服强度 ,以T7 处理效果最为显著; 而T6, T7处理均可提高铸件的韧性 ,并且提升范围较大; T7处理与 T5,T6处理相比,可同时显著提高铸件的强度与韧性 , 而T5,T6处理在某一方面对铸件性能提升较为明显。
从以上的研宄表明,通过T5热处理,高真空压铸Silafont36合金中共晶硅晶粒发生粒化、球化,能够有效的提高铸件韧性。从验证实验结 果可以看出,铸件经优化的T6、T7工艺,不仅能够获得较高的强度,并且可以获得较高的伸长率,满足了合金对高强韧的要求。
验证实验铸件的金相组织如图图11所示。
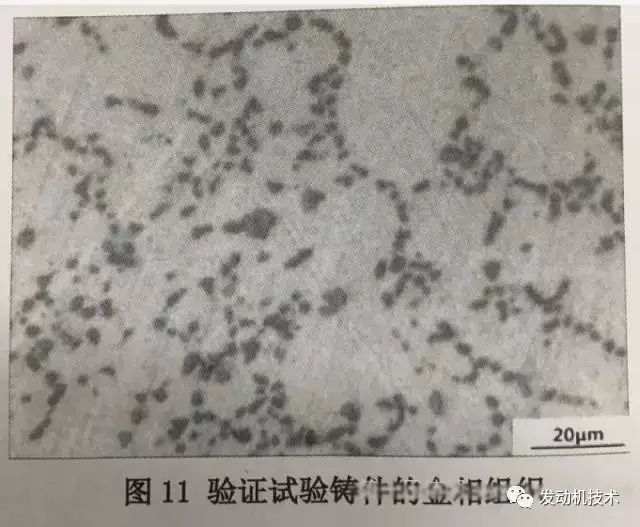
从图 11 中可以看出 , 铸态下的共晶硅树枝晶状组织在高温固溶处理过程中发生了缩颈、熔断、钝化、粒化和球化,并且分布均匀在基体上,硅颗粒的粒化和球化减轻了其割裂基体和承载时应力集中的情况,使合金的强度和伸长率都有提高;同时团状富铁相组织在高温固溶时发生钝化,也有利于提高合金的性能;高温固溶后的淬火,在α-Al基体中的Si相和Mg相形成过饱和固溶体,在人工时效的过程中,析出Mg2Si强化相,其析出过程为:球状GP区-针状β' '相-棒状β'相一片状平衡相 β (Mg2Si) , 其中 β' ' 相对合金具有强化作用,而 β'相的强化作用最强,当针状的 β' '相基本转变为棒状的 β'相后,材料的抗拉强度和硬度达到峰值。在实际生产中,T6、T7应用更为广泛,因为通过高温固溶,不仅可以使共晶硅晶粒发生粒化和球化,同时还可以将合金中的富Mg相充分溶解在α-Al固溶体内,淬火后,固溶体内Mg元素形成过饱和状态,经过完全人工时效处理,过饱和的元素以Mg2Si强化相的形式充分析出,可以大幅提高铸件的强度,从而使合金获得具有高韧性和高强度的力学性能。
3 结论
采用高真空压铸,开发了压锩Silafont36合金汽车底盘结构件,并对产品实施了不同工艺的热处理,获得了结论为:
(1) T5处理可显著提高铸件的强度,相对比铸态力学性能,抗拉强度可提高24%,屈服强度可提高45%,而铸件的伸长率则相对铸态降低不明显,甚至稍有提高,铸件的个别位置甚至可达到4.5%。
(2)T6处理降低了铸件的极限抗拉强度,但可显著提高铸件的韧性,相对铸态,T6处理后,铸件抗拉强度降低了12.2%然,而最小屈服强度则提高了17.8%;铸件的伸长率经T6处理最大可达到8.4%,最小值也达到了4.2%。
(3)T7处理一方面可提高铸件的强度,同时可提高铸件的韧性,T7处理后,铸件的最小屈服强度相对铸态提高了53%,伸长率最小值达到了4.8%,最大值达到了9.1%。
(4)对不同热处理方式,可总结为T5处理对提高铸件的强度有利,而T6处理则有利于提高铸件的韧性,T7处理同时兼具T5,T6优点,可同时提高铸件的强度和韧性。
参考文献
[1]卢宏远,卢敏,宋青,等.汽车结构件的压铸[J].特种铸造及有色合金,2012,32(3):251一254
[2]万里,潘欢,罗吉荣.高真空压铸技术及高强韧压铸铝合金开发和应用的现状及前景[J],特种铸造及有色合金,2007, 27(12):939一942.
[3〕万里 , 刘学强 , 胡祖麒, 等 . 高真空压铸 AISi10MgFe 合金的组织和力学性能 [J] . 特种铸造及有色合金 2014,34(5):499一503,
[4〕团张百在, 刘学强, 万里, 等. 含量对 AIS110MgMnFe 压铸件组织和性能的影响[J).特种铸造及有色合金, 2016, 36(8):829一832.
[5]张百在, 刘学强, 万里, 等. 型腔真空度及热处理对 AISiMgMn 压铸件性能的影响[J] . 特种铸造及有色合金, 2016 , 36(7):673一676.
[6]THIRUGNANAMA,SUKUMARANK,PILLAIUTS,et al. Effect of Mg on the fracture characteristics of cast AL-7Si-Mgalloys〔J]. Mater. Sc. and Engg•,2007,A 445 446:405 406.
[7]徐飞跃, 安肇勇 , 万里, 等. 压铸高强韧铝合金汽车底盘结构件的组织与力学性能[J]. 特种铸造及有色合金,2016,36(6):616一619.